Chamber Filter Plates
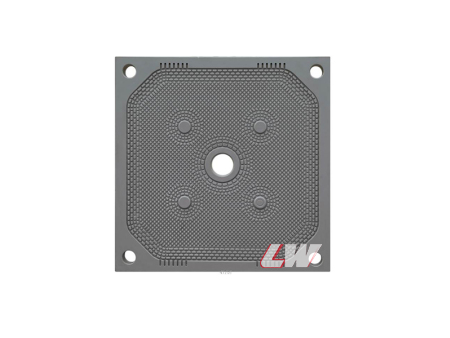
Our chamber filter plates consist of multiple independent filtering units. Each unit is equipped with a high-quality filtering medium such as filter cloth, filter paper, or other porous materials. Housed in a robust, sealed frame, these units guarantee a secure, leak-free filtration process even under high-pressure and high-temperature conditions.
Key Features
✅ Multi-convex reinforced design ensures flat surfaces that prevent material leakage during filtration.
✅ Variable cross-section design with flower-shaped conical point structure reduces filtration resistance.
✅ High temperature and pressure resistance with excellent corrosion and sealing properties.
✅ Fast filtration speed with uniform filter cake washing.
✅ High solid material recovery rate with clear filtrate production.
✅ Simple structure with low failure rate and easy maintenance.
Material Selection
Chamber filter plates are manufactured from materials selected based on the chemical properties and temperature requirements of the process media. Common materials include:
- Stainless Steel: Ideal for high temperature and corrosive environments.
- Polypropylene & Polyvinyl Chloride (PVC): Excellent for applications requiring chemical resistance and durability.
Technical Specifications
Parameter | Specifications |
---|---|
Material Options | PP, PVC, SS304/316, cast iron |
Temperature Range | -10°C to 120°C (varies by material) |
Pressure Resistance | Up to 25 bar |
Filtration Area | 0.5–2.0 m² per plate (customizable) |
Cake Thickness | 20–50 mm |
Applications of Chamber Filter Plates
Industry | Use Cases |
---|---|
Water Treatment | Municipal wastewater, industrial effluent purification, sludge dewatering. |
Chemicals | Catalyst recovery, acid/alkali filtration, polymer separation. |
Oil & Gas | Drilling mud treatment, refinery waste filtration, lubricant purification. |
Food & Pharma | Juice clarification, dairy processing, API purification, sterile filtration. |
Mining | Tailings dewatering, mineral concentrate extraction. |
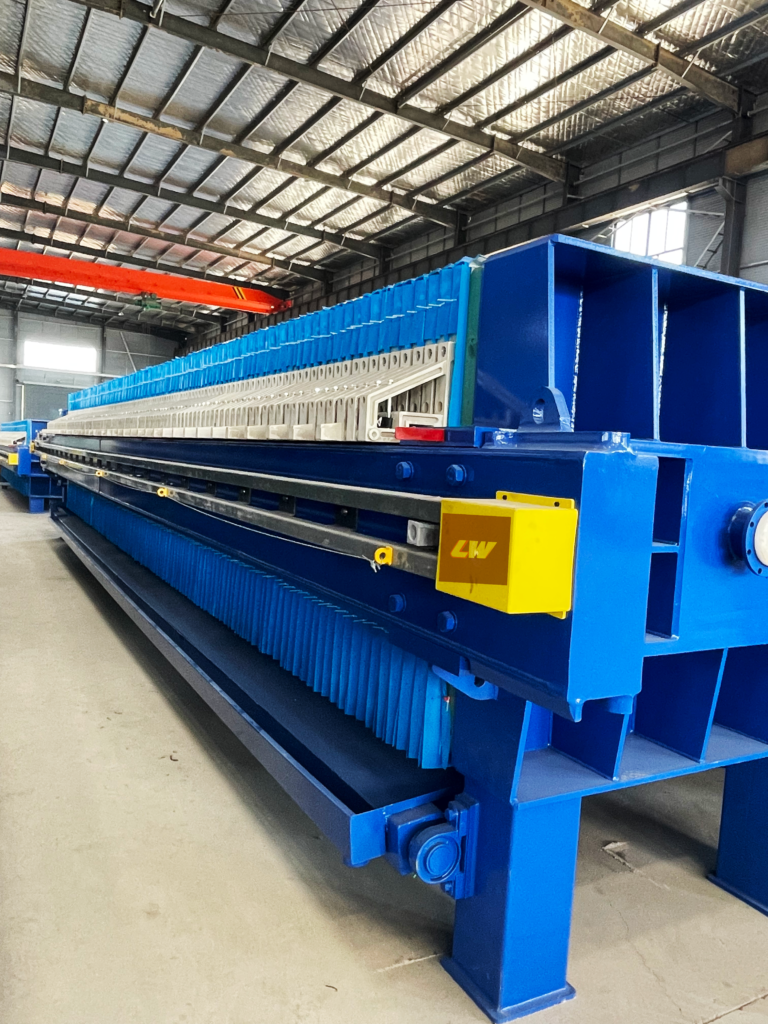
Get a Quote
Contact our team of filtration specialists today to discuss how our filter press solutions can address your specific solid-liquid separation challenges.
Request Instant Quote
Customized Solution for Your Project
86 189 5282 5752
support@lowayequipment.com
Advantages of Chamber Filter Plates
High Efficiency Filtration
Chamber filter plates achieve efficient solid-liquid separation with fast filtration speeds and clear filtrate production.
Easy Maintenance
The design allows for easy disassembly and cleaning, making maintenance simple and straightforward.
Automated Operation
Modern chamber filter plates are typically equipped with automated control systems, enabling unmanned operation.
Durability
High-quality materials and structural design give the filter plates a long service life with low failure rates.
Advanced Technology & Design
Our chamber filter plates incorporate innovative design elements to maximize performance
- Multi-Boss Reinforced Structure: Enhances the structural integrity and durability during high-pressure operations.
- Precision CNC Processing: Ensures flat surfaces and a uniform finish, preventing material leakage during filtration.
- Variable Cross-Sectional Design: Features a tapered, round dot pattern that minimizes filtration resistance, leading to faster processing and a more consistent filtrate flow.
Common Questions
Have More Questions? Our technical team is ready to provide detailed, personalized guidance.
Q1: Chamber vs. Plate-and-Frame Filter Presses – What’s the difference?
Chamber Plates: Two recessed plates form a chamber; better for high-solid slurries, durable, and efficient.
Plate-and-Frame: Uses alternating plates and frames; simpler cloth replacement but less efficient.
Q2: How do chamber filter plates work?
Under the pressure from the feed pump, liquid is forced through a filter medium that captures solid particles. The resulting filter cake is periodically cleaned through a reverse-flow backflushing process to maintain efficiency.
Q3: How often should I backwash chamber filter plates?
Depends on slurry solid content. Typically every 5–10 cycles or when flow rate drops by 20%.
Q4: Can these plates handle acidic or alkaline fluids?
Yes! Select PP for mild acids/bases or stainless steel for aggressive chemicals.
Q5: Can chamber filter plates handle high-temperature applications?
Yes, depending on the material of construction. Stainless steel filter plates are particularly suitable for high-temperature applications in industries like petrochemical processing.
Q6: What filter cloth material is recommended?
Polyester, nylon, or PTFE-coated fabrics, depending on temperature and chemical exposure.
How it works
We provide one-stop service of solid-liquid seporator planning, design, consultation, construction, equipment manufacturing, installation, commissioning and training. We are involved in complete sets of sludge dewatering projects for various industries.
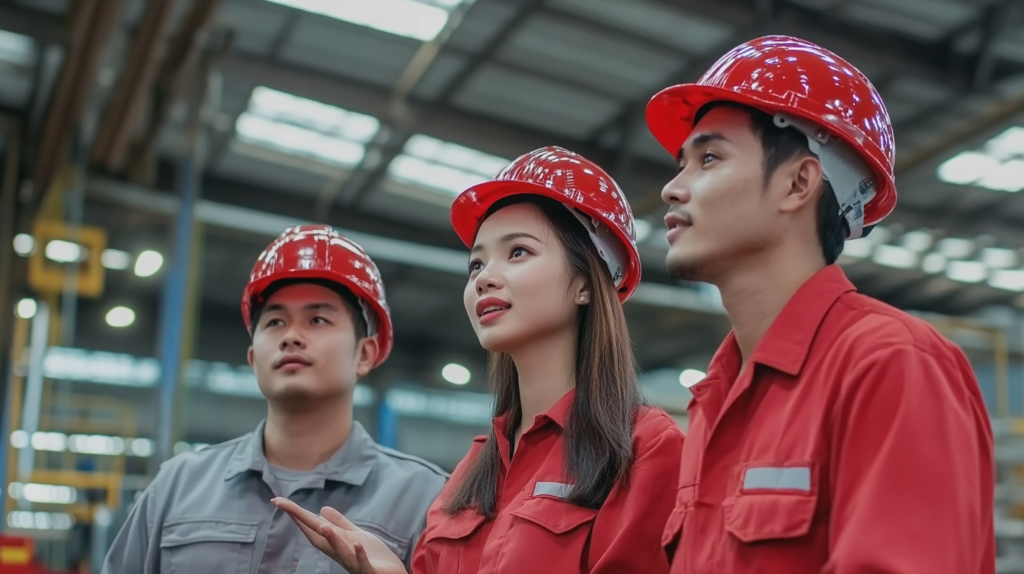
Consultation what you need.
We do not aim to achieve maximum profit and do not reduce the quality of our products by catering to the market with low prices. We are happy to provide high quality tailor-made filtration equipment to you.
Production the filter press equipment for you
Our professional and advanced production technology, excellent manufacturing process, and perfect testing ensure that your equipment fully meets the quality acceptance standards.
Installation and commissioning equipment
Our skilled installation team installs this equipment for you in strict accordance with the construction drawings and construction process steps. Experienced technicians will debug and analyze the average results on site to achieve the best results and meet the needs of use.
After sales service
Our technicians patiently and meticulously answer all your questions and provide guidance and suggestions through messages, phone calls, videos, and arriving at the site.